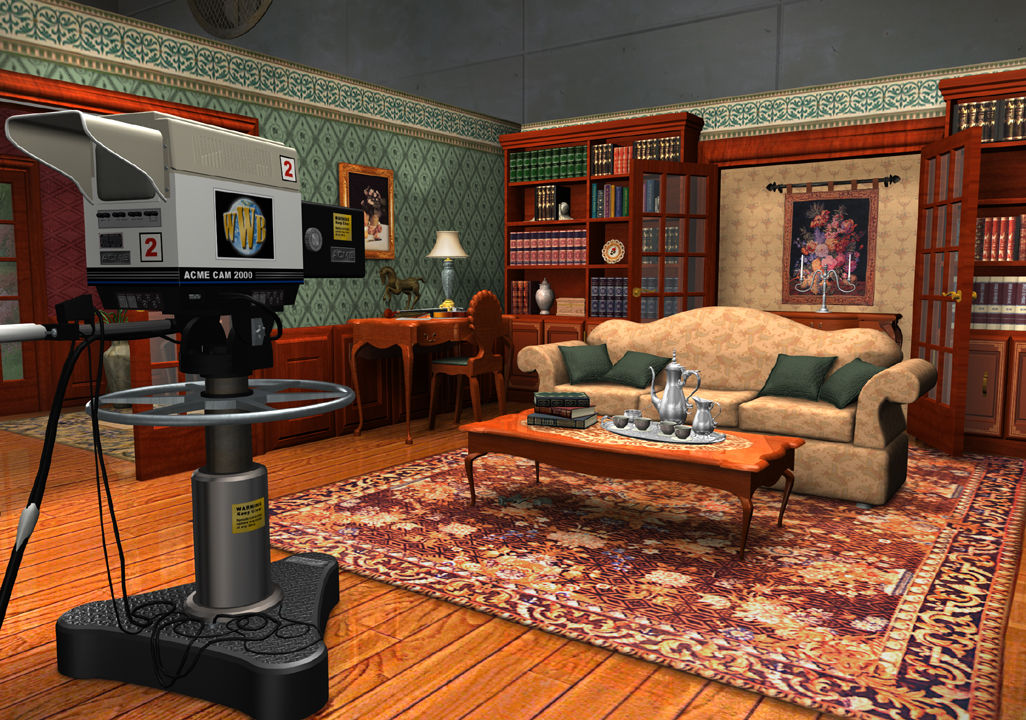
nancy drew clue crew
"Kapa (Bark Cloth)”
by: Unknown Author(s)
Along with taro plants, chickens, pigs and dogs, the first immigrants brought with them to Hawai’i roots of wauke, the paper mulberry tree, so they could continue the ancient tradition of making cloth out of bark. This cloth, called kappa (tapa in other parts of Polynesia), was used to make the pa’u (wrap-around skirt) worn by women, the malo (loin cloth) worn by men, bedding, ceremonial robes, and the wrappings in which the bones of dead loved ones were buried.
Making kappa was a long, labor-intensive process. Wauke trees, which grow best in moist areas were planted near streams or taro fields, and carefully tended and pruned so that the trees grew straight with no side branches. After 8 to 12 months, when the trunks were between one to two inches in diameter, they were cut down. The outer bark was stripped away, and the fibers of the fine white inner layer, called bast, were removed. The bast was soaked in water for up to ten days, then beaten with a wooden mallet. Then they were soaked again and allowed to ferment.
Some of the fibers were twisted into cords to be used in fish nets and to tie building materials together. The fibers that were to be used for cloth were spread out in layers. As they dried, the layers formed a single mass called mo’omo’o. This mass was laid out on smooth rocks and pounded with wooden mallets, then allowed to dry. Once dry, they could be stored until enough mo’omo’o had been accumulated to make apiece of cloth. The bundles were then soaked again, pounded, then wrapped in banana leaves and left to ferment. The fermentation process resulted in a matted, seamless mass of soft, resilient, white fibers.
The bundle was then laid out on a long, flat wooden anvil and pounded flat with four-side wooden beaters. The cloth was soaked, then doubled over and beaten again. Then the process was repeated. The wooden beaters, or i`e kuku, which were used in the final stage were often carved with intricate patterns which were thus beaten into the cloth, leaving a distinctive “watermark” which could be seen when the kappa was held up to the light. With each beating, the size of the cloth expanded, until it was finally dried in the sun.
The white cloth which resulted was then died with pigments from a variety of plant sources, such as berries, bark, roots and even mud from taro fields. Geometric designs were stenciled or stamped on the cloth, which was often stored with aromatic oils and seeds to give the cloth a pleasant smell and to mask the odor of the fermented fibers.